By the end of 2017, we were aproached by Unilever to produce some CGI scenes for a new "Danoninho" film.
The job consisted of 2 small scenes of fluid simulation and 1 scene of particle simulation for the product "Danoninho".
We already had the scene setup from the previous job (bkg, models, rig, and light setup), but we had only 2 weeks to deliver everything. The main work was doing the character animation (done by a freelancer animator in Maya) and the simulations.
I did all the FX in Houdini, and rendered in Houdini with Mantra. The composite was done in Nuke.
We already had the scene setup from the previous job (bkg, models, rig, and light setup), but we had only 2 weeks to deliver everything. The main work was doing the character animation (done by a freelancer animator in Maya) and the simulations.
I did all the FX in Houdini, and rendered in Houdini with Mantra. The composite was done in Nuke.
The deadline was tight (2 weeks), so we had to come with clever solutions to deliver the project on time.
The first problem we encountered was keeping the fluid level in a determined height. To tackle that, we created a custom solution to fill the bottle with fluid until certain height wa reached. The solution was quite successful for the first shot, but not so much for the second. Due to the time constraint, we had to work with the simulation we had.
The second problem was the sugar simulation and rendering, since we wanted to get a believable result straight from Mantra. We tried to go straight to a physical simulation, so we built a hybrid solver, to calculate the air-particle interaction and the particle-air feedback.
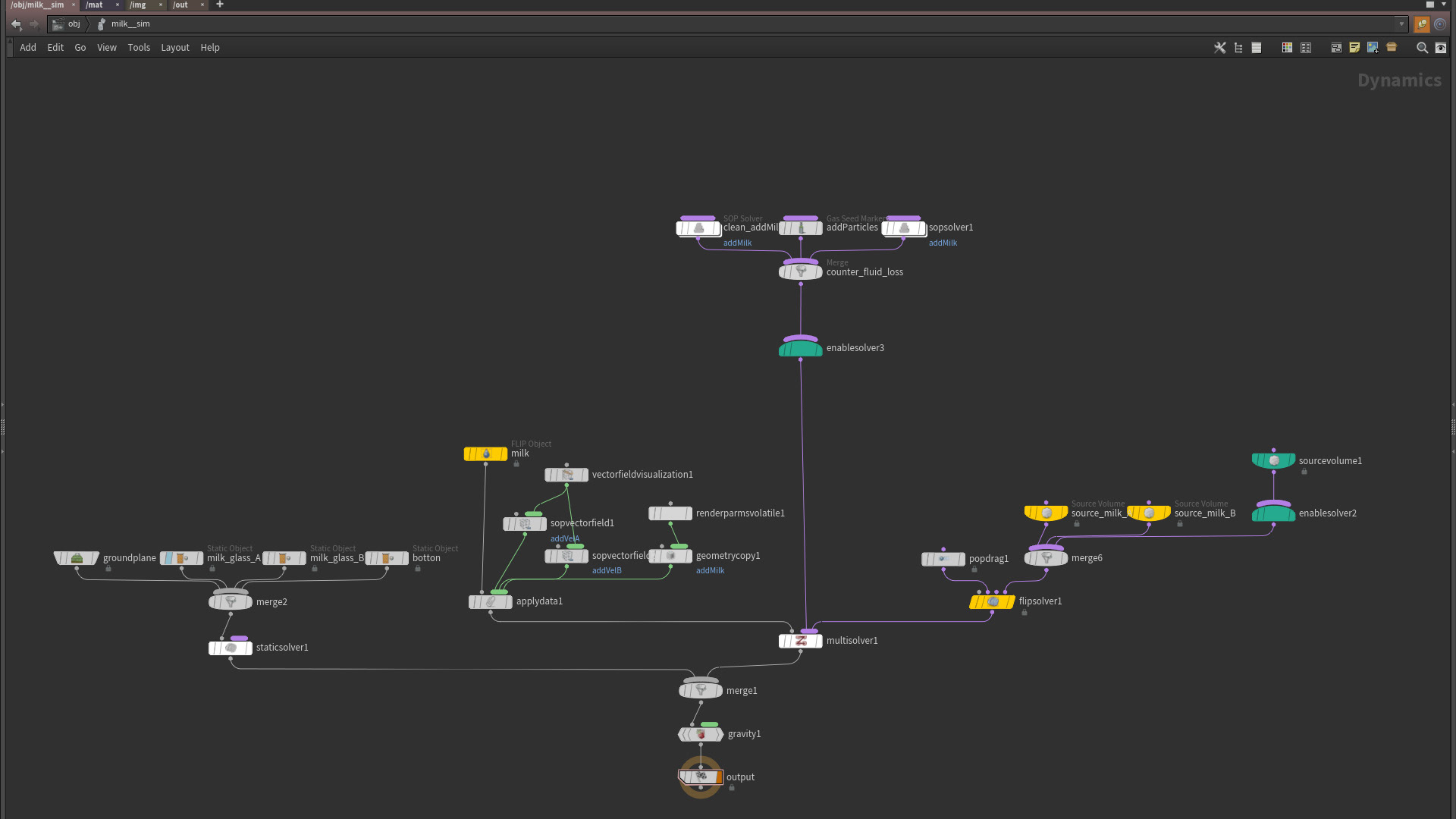
Shot 2 simulation setup with the bottle filler solver.
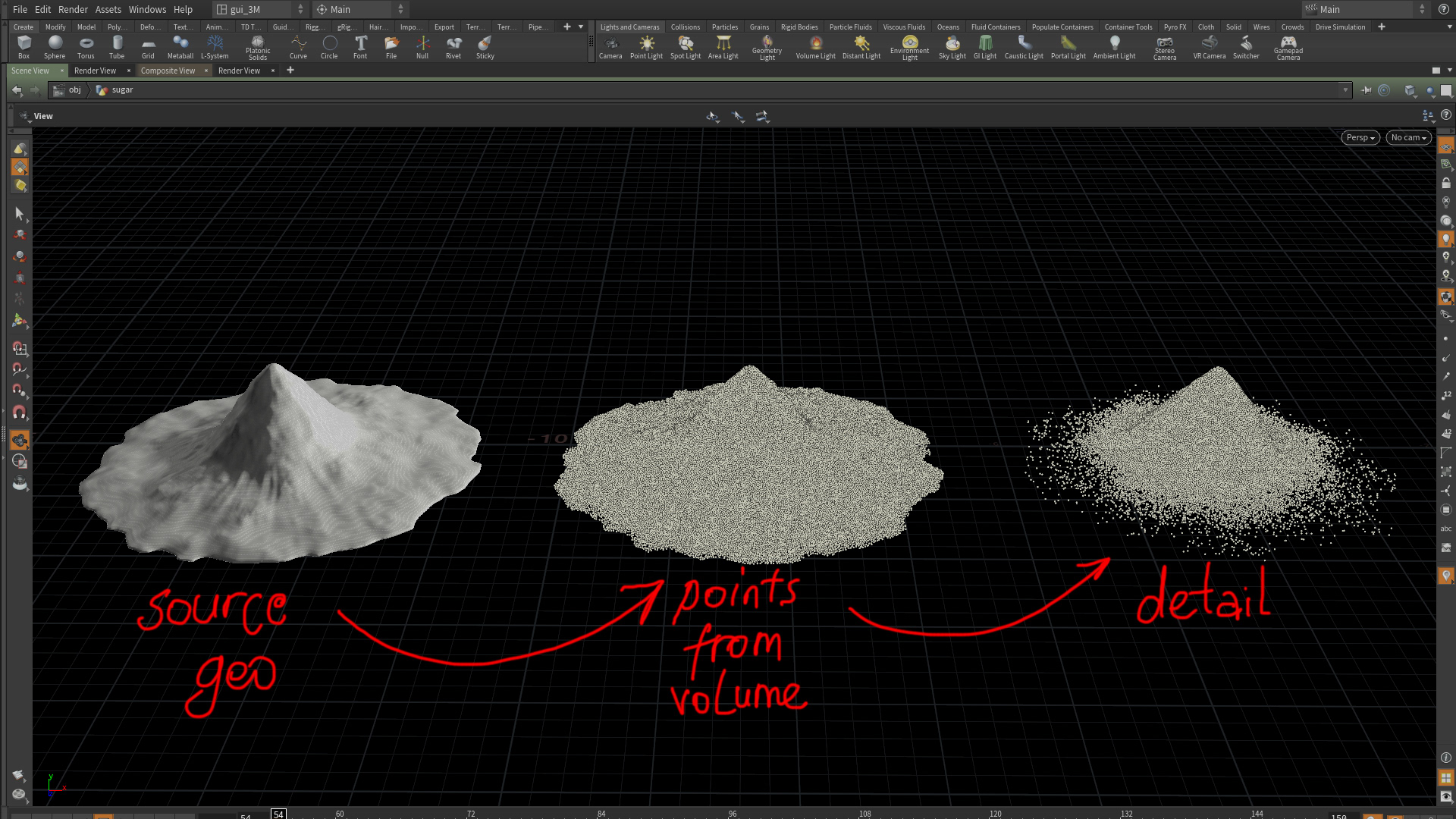
The process used to build the sugar pile.
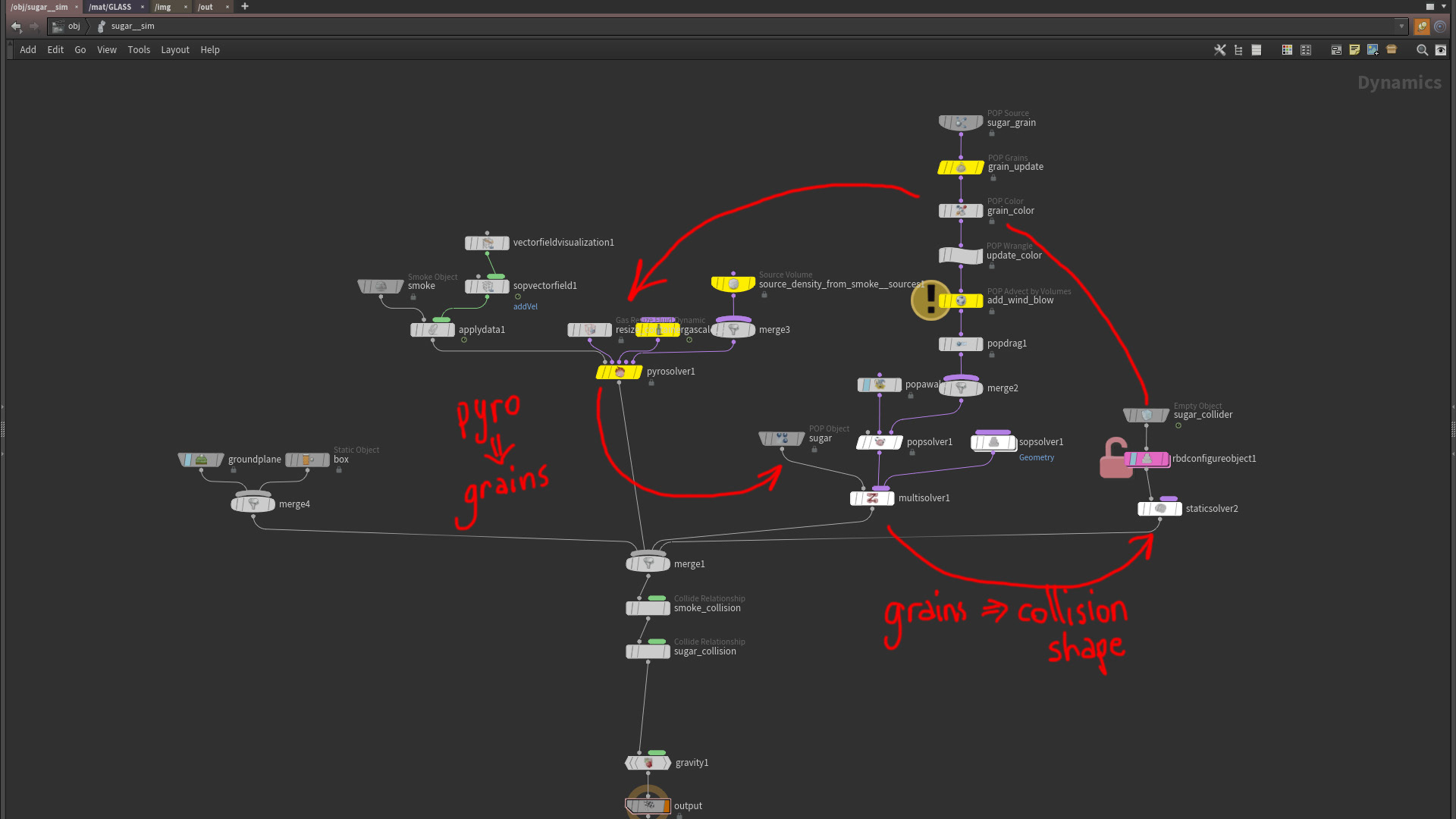
The hybrid solver, used to give the particle->air feedback.
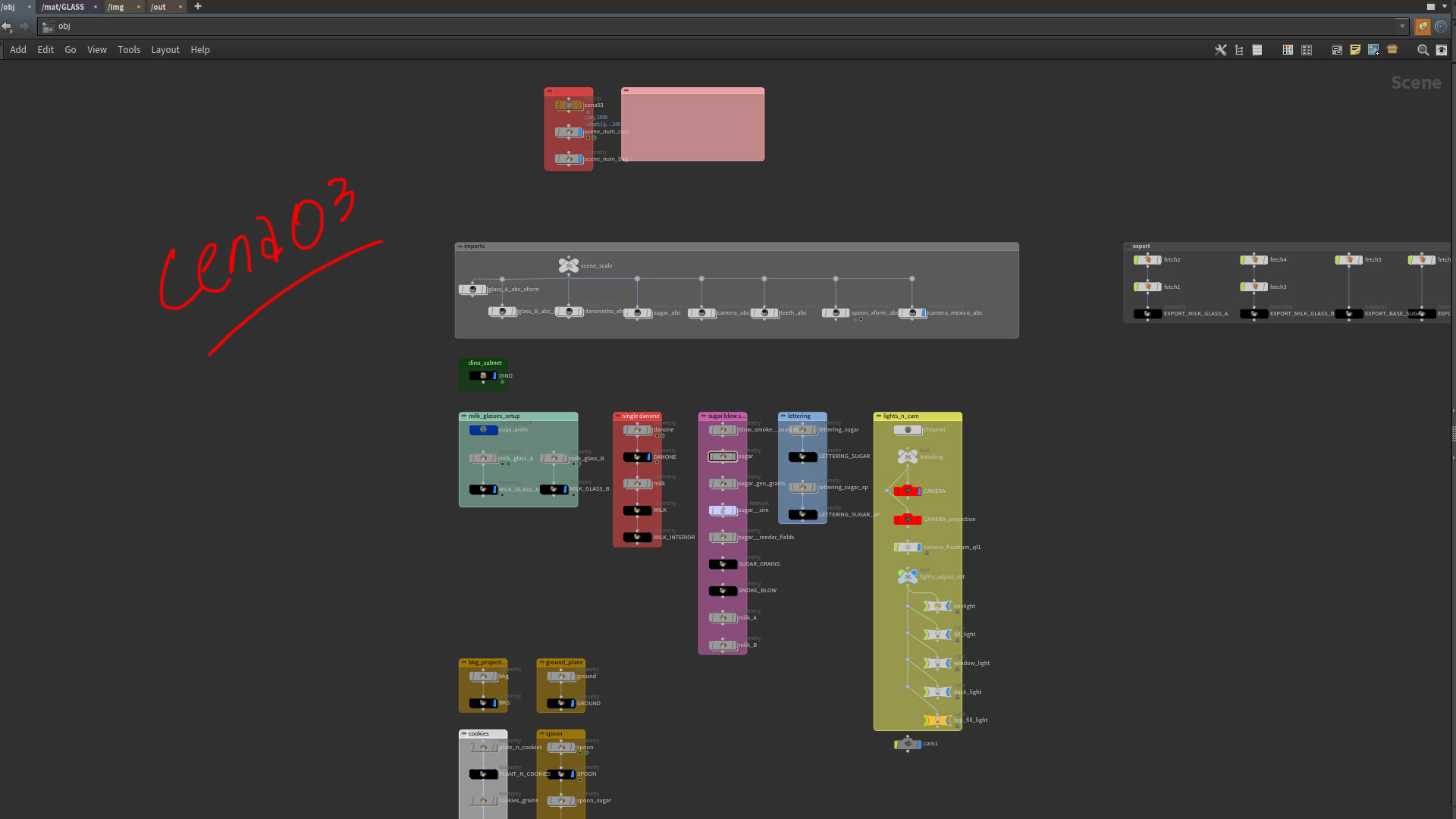
Scene 3 network.
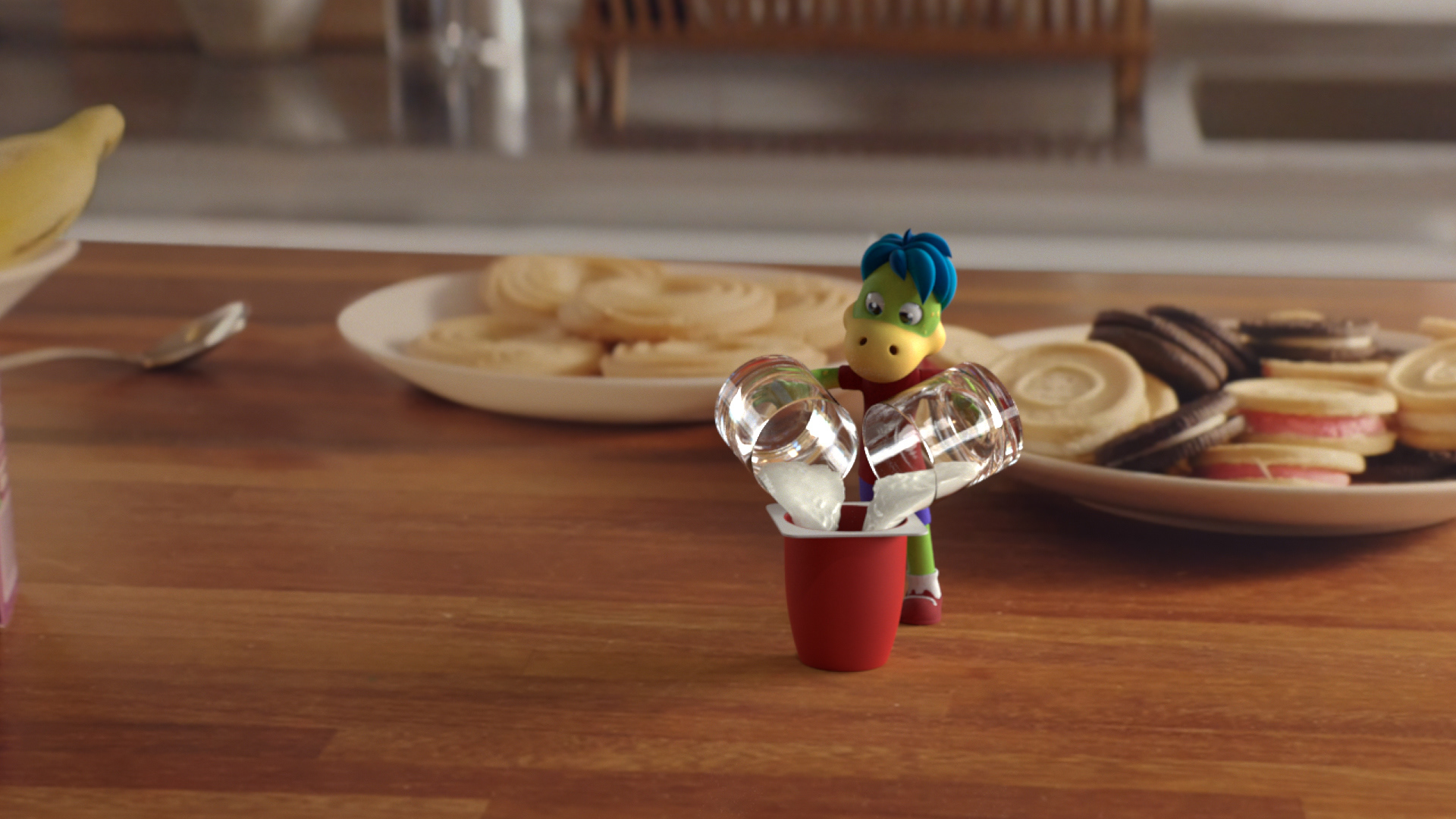
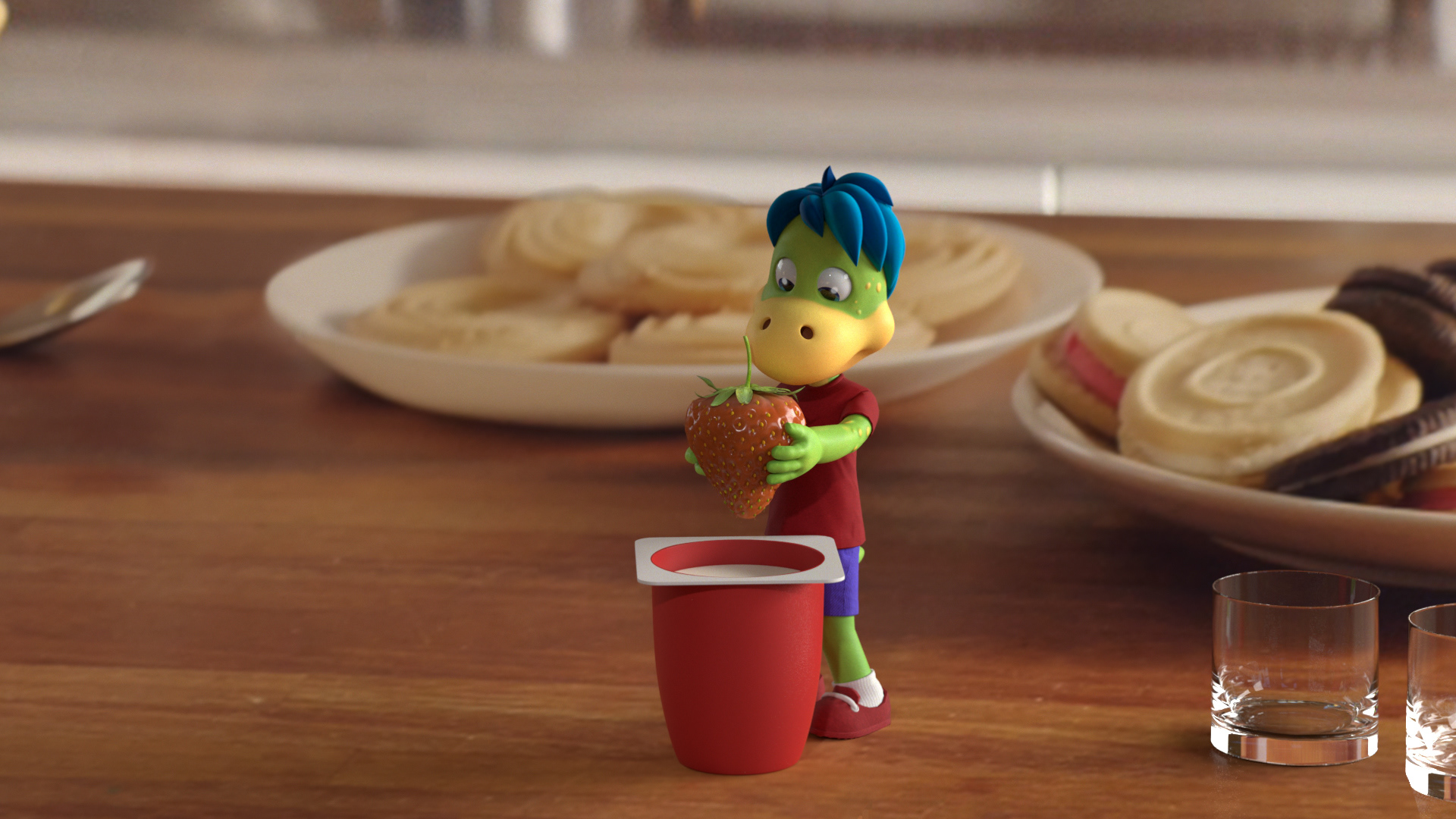
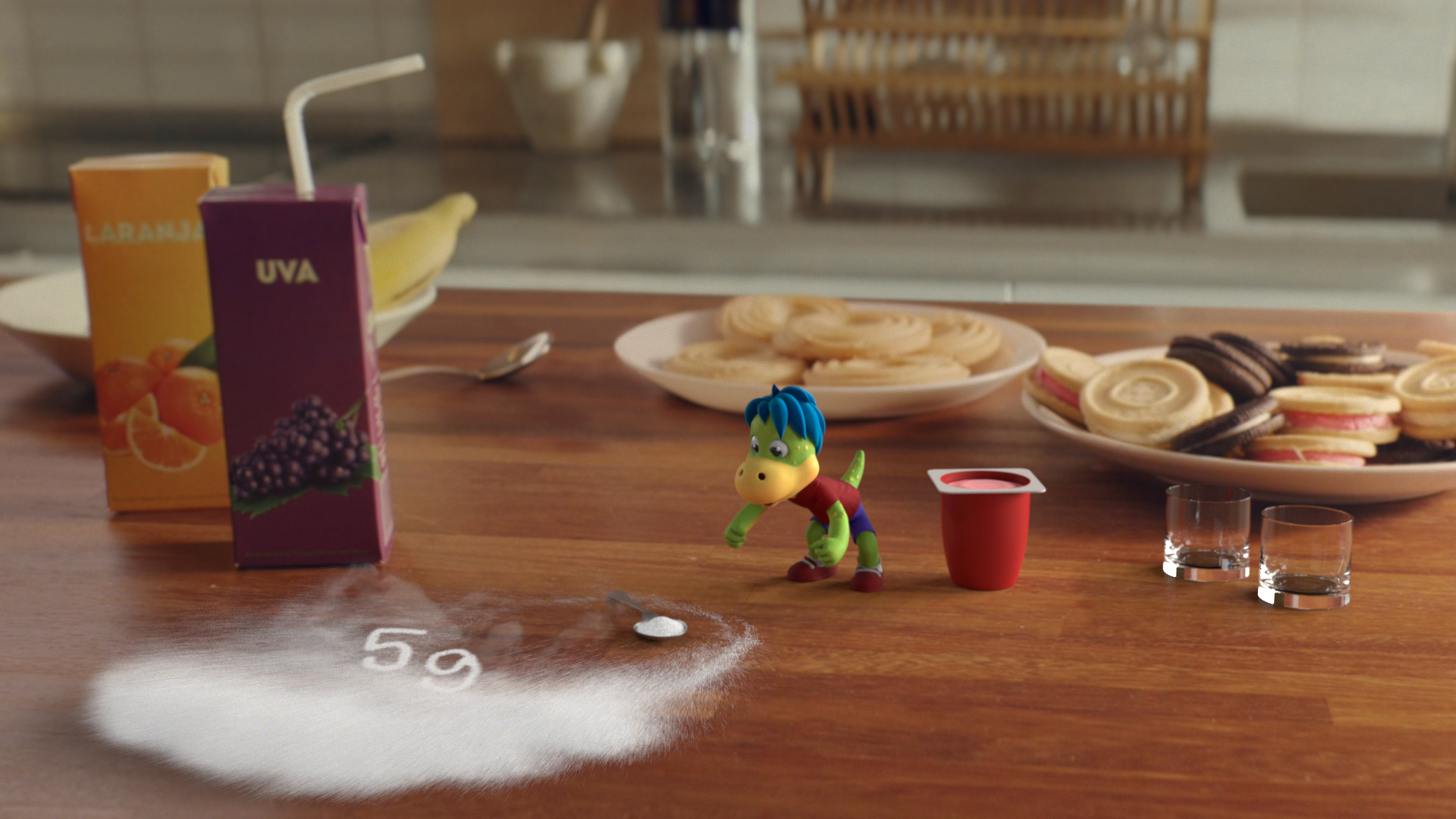